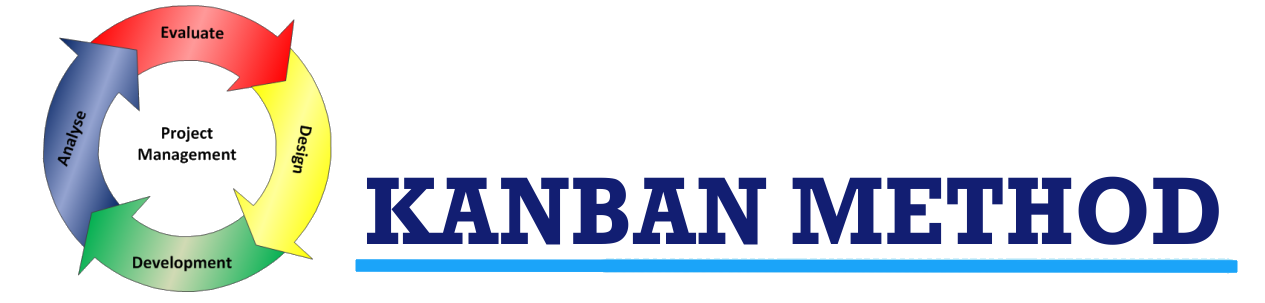
Kanban is getting a lot of buzz these days as a product development method because, according to its fans, it can overcome problems that stymie methodologies like Scrum and Waterfall. But with its Japanese origins and Zen-like aura, Kanban is mysterious to many people. One of the most quoted sayings in Kanban is: “Stop starting and start finishing.” Sounds profound, but how do you implement that?
If you feel the need for some Kanban decoding. you’ve come to the right place. We have compiled the complete guide to Kanban for newbies including tips and wisdom from some of the foremost practitioners and teachers of Kanban.
First, a note on pronunciation: As a Japanese word, the authentic pronunciation of Kanban is KAHN-ban. That is also the preferred English way to say it, over CAN-ban, which is also occasionally used.
Origins of Kanban: From the Grocery Store to the Factory Floor
Understanding how Kanban originated will help you make the most of this project framework. Kanban was developed as an inventory-control system for just-in-time manufacturing by an engineer named Taiichi Ohno at Toyota in the 1940s.
Ohno was inspired by the way American grocery stores stocked their shelves. Customers would buy what they needed, and the store would restock based on what had sold and expectations of demand. The stores realized it didn’t make sense to keep more on hand than needed to meet customer demand.
Matching inventory to demand increased efficiency, reduced waste, and improved the quality of operations for grocers. While it may sound obvious, this was – and is still today – a departure from systems based on top-down processes determined by management, using a fixed schedule or running inventory based on vendor priorities.
Kanban Harnesses the Power of Visual Information
Instead of inventory arriving without regard to what was selling, those Japanese grocery stores adjusted their orders based on what products were depleted. They leveraged the visual cue of shelves running low. Toyota took this practice and used it to improve its manufacturing system. Rather than work being pushed onto a team, with Kanban work was pulled in response to demand, similar to the way the grocery stores restocked their shelves.
Kanban itself is a Japanese word that means sign, card, or billboard. At Toyota, assembly line workers used physical tokens as signals for just-in-time inventory replenishment and inventory control. In modern times these are printed bar codes attached to a physical object such as a tray or pallet.
The Kanban System Makes A Leap Beyond Manufacturing
Kanban was well established in physical goods industries such as manufacturing and distribution. To adapt its use to intangible goods work such as software developed required adaptation, physical cards had to be replaced with visual signals often shown as numbers on a board or implemented with software. Virtual Kanban systems, as they were known, were used to improve the agility of existing software development processes, and the technique became accepted with the Agile software development movement. Today, it is used in every sector from retail to healthcare, and many people find it an invaluable tool for managing their own to-do lists.
“All teams and all projects can use Kanban,” said Grady Brumbaugh, a Kanban trainer at The Digital Innovation Group. “The work environment where Kanban thrives is one where delivery timelines are tight and those prioritizing the work can make a stack-ranked based decision.”
Kanban is a Mindset and a Method
Kanban is a project tool, but it’s also a mindset. It’s about making sure you as a project manager choose the right things, at the right time, focusing on what should be done now. What should be left until later. And, what should we not be done at all. Kanban asks you to pull work when you have capacity rather than push it onto workers and overburden them. It also asks you to think of your project as a sequence of activities through which work flows. Focusing on flow of work to completion becomes a key concept with Kanban.Kanban helps manage the flow of your project process, whether your inputs are widgets, car parts, documents, or software code. You need to have those key pieces in the right place and at the right time. If you don’t, bottlenecks, waste, and delays develop. This holds true whether you are missing a critical ingredient or have too much of something. Kanban ensures your process flows smoothly.
Six Core Kanban Principles
David J. Anderson was so pleased with the results he found while using Kanban systems at Microsoft in the mid-2000s, that he placed them at the heart of his method for driving continuous improvement within companies. Toyota calls this concept Kaizen. Anderson chose to name his method for continuous improvement after the Kanban systems that enabled it. In his book, “Kanban - Successful Evolutionary Change for Your Technology Business,” he described six key practices that drive these outcomes.
- Visualize your work
- Limit work in progress (WIP)
- Manage flow
- Make policies explicit
- Implement feedback loops
- Improve collaboratively, evolve experimentally
Among those, the first three are the most important.
Visualize workflow - A centerpiece of Kanban is a board that represents the workflow, the legacy of the Toyota signboards. This can be a bulletin board, white board, or an online tool. Columns represent the steps in your process and under each, you list the relevant tasks or work items. These can go on cards or Post-it notes if you are using a physical board.
A basic Kanban board organization would be: To Do, Doing, Done. This equates to a Kanban “three-bin system” found in a manufacturing setting for parts at the point of use, parts in inventory, and parts at the supplier - a system that makes sure workers never run out of parts.
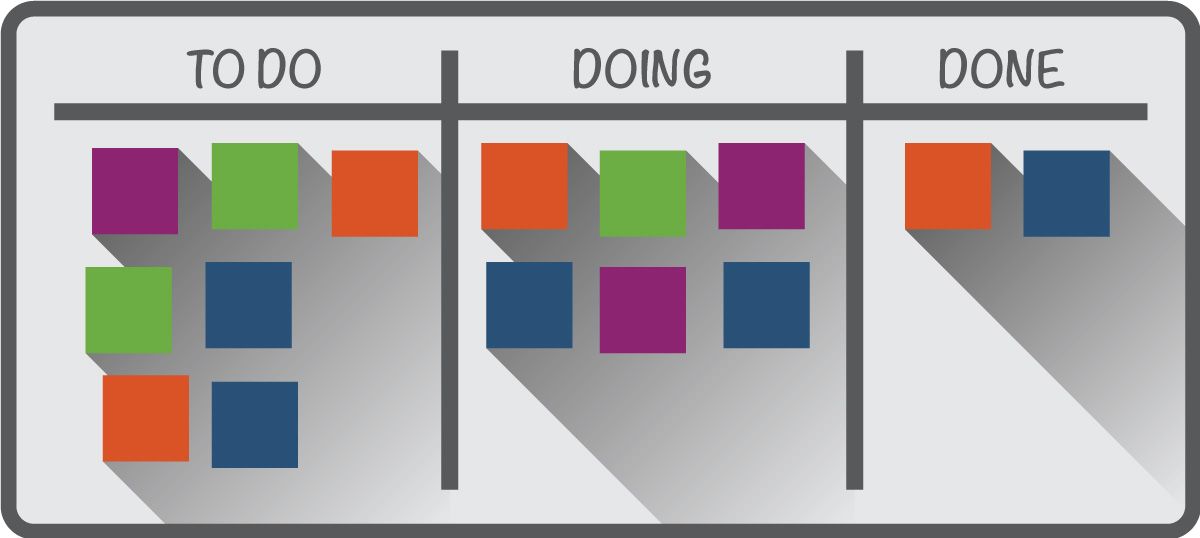
But a Kanban board can also work for more complex processes with many steps. Cards can be color-coded based on work type if you’re working on a complicated project.
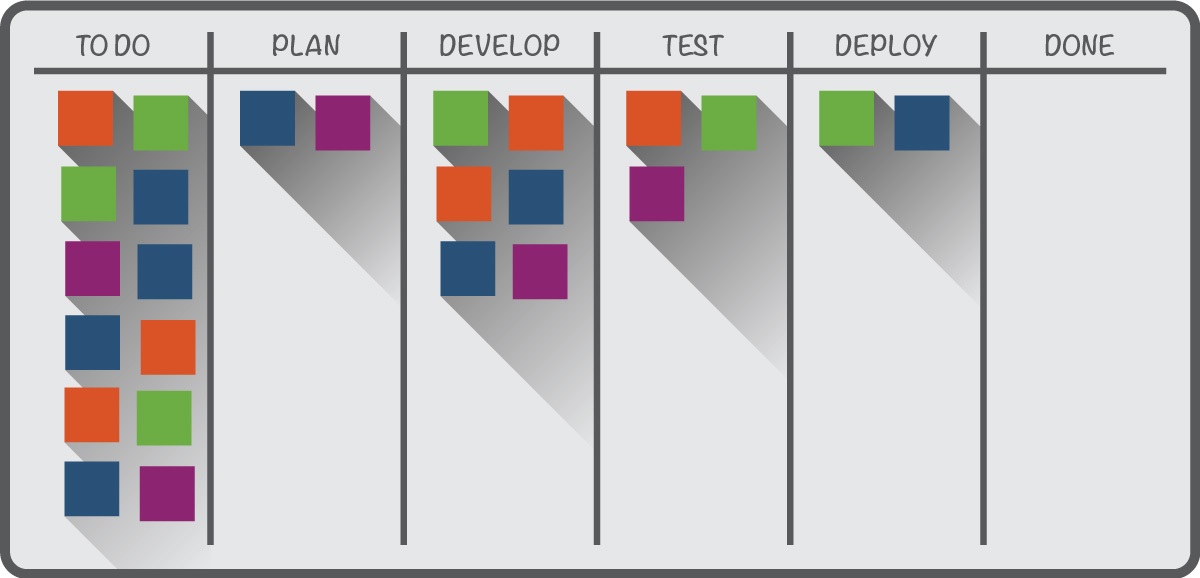
When everyone on your team sees the work in this concrete way, it becomes obvious how the work is progressing and where problems exist. Visualizing the workflow is critical to Kanban’s effectiveness, but Kanban experts caution that a common pitfall is to believe that having a board is all it takes.
“Having a Kanban board, or using a tool...does not mean that you are doing Kanban, yet.
Do not fall into that minimalistic trap, it is good to consider using tools, but learn the principles, values, and tools of Kanban before actually experimenting with them. An overly simplistic view of Kanban leads many to failure,” said Joseph Hurtado, a project manager and Kanban trainer with AgileLion Institute.
Limit Work In Process (WIP) -This is a principle that can be hard for overachievers to embrace, but Kanban believes you can be more effective and accomplish more by trying to do less. While this seems counterintuitive, most of us have experienced that we can only take on so much and execute it to a high standard on time. Any more and something slips.
Kanban practitioners say the WIP limit does magical things for efficiency by having team members in each stage of the workflow handling only the ideal number of tasks at once. They do not pull more work until they complete something. No more headless-chicken mode!
“Kanban is the perfect tool to limit work in process, which is proven to speed up total throughout…. Personal Kanban brings that benefit to your personal to-do list, everyday, and just might be the new secret of highly effective people,” said Joe Justice, President of Scrum Inc.
The WIP limits are implemented by allowing only a certain number of tasks in each column of your Kanban board. This requires prioritization of the work. “Slack is the only way we can improve ourselves... Lean Kanban is the only method that actually puts this concept as a pillar of its approach and manages towards it. Limiting WIP is the only way to improve,” said Daniel Doiron, Lean Kanban trainer at CC Pace.
Manage Flow - One strength of Kanban is that you start where you are, with your existing process. You don’t have to change everything overnight to a process plucked from a Harvard Business School case study.
Kanban enables you to improve continuously by creating awareness and sparking discussion of how to evolve your process, enabling you to keep what’s working and avoiding an implosion from too many big changes at once. Instead, you make incremental improvements by reviewing where inefficiencies lie and learning from mistakes.
In Kanban, the workflow should minimize lead times, maximize the delivery of value, and be as predictable as possible, according to LeanKanban Inc. CEO David Anderson in the Essential Kanban Condensed ebook. Using Kanban will enable you to spot bottlenecks, get rid of them quickly and prevent them arising again.
See how easily the Kanban board shows bottlenecks?
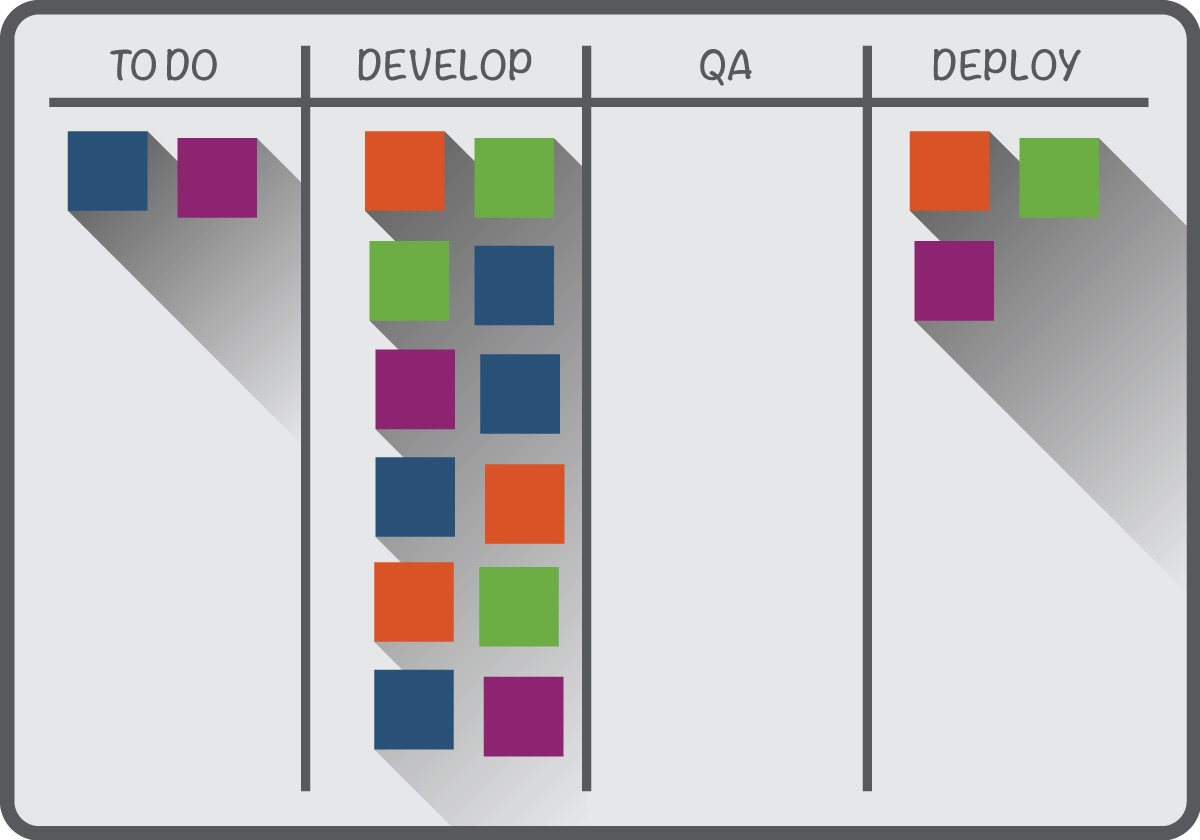
Remember: Pull, Don’t Push, the Work
Another important aspect of managing flow in Kanban is understanding that the ideal number of tasks will vary at different points in your process. A software developer may only be able to code one feature at a time while a technical editor may be able to work on multiple sets of documentation. This can become a problem if they produce at different rates and even give rise to friction.
Remember the key “pull” concept in Kanban is that each team member pulls work when he or she is ready. (The grocery store doesn’t order more inventory until it’s running low.) If needed, you can add buffer columns on your board with limited capacity to prevent work from getting pushed onto team members.
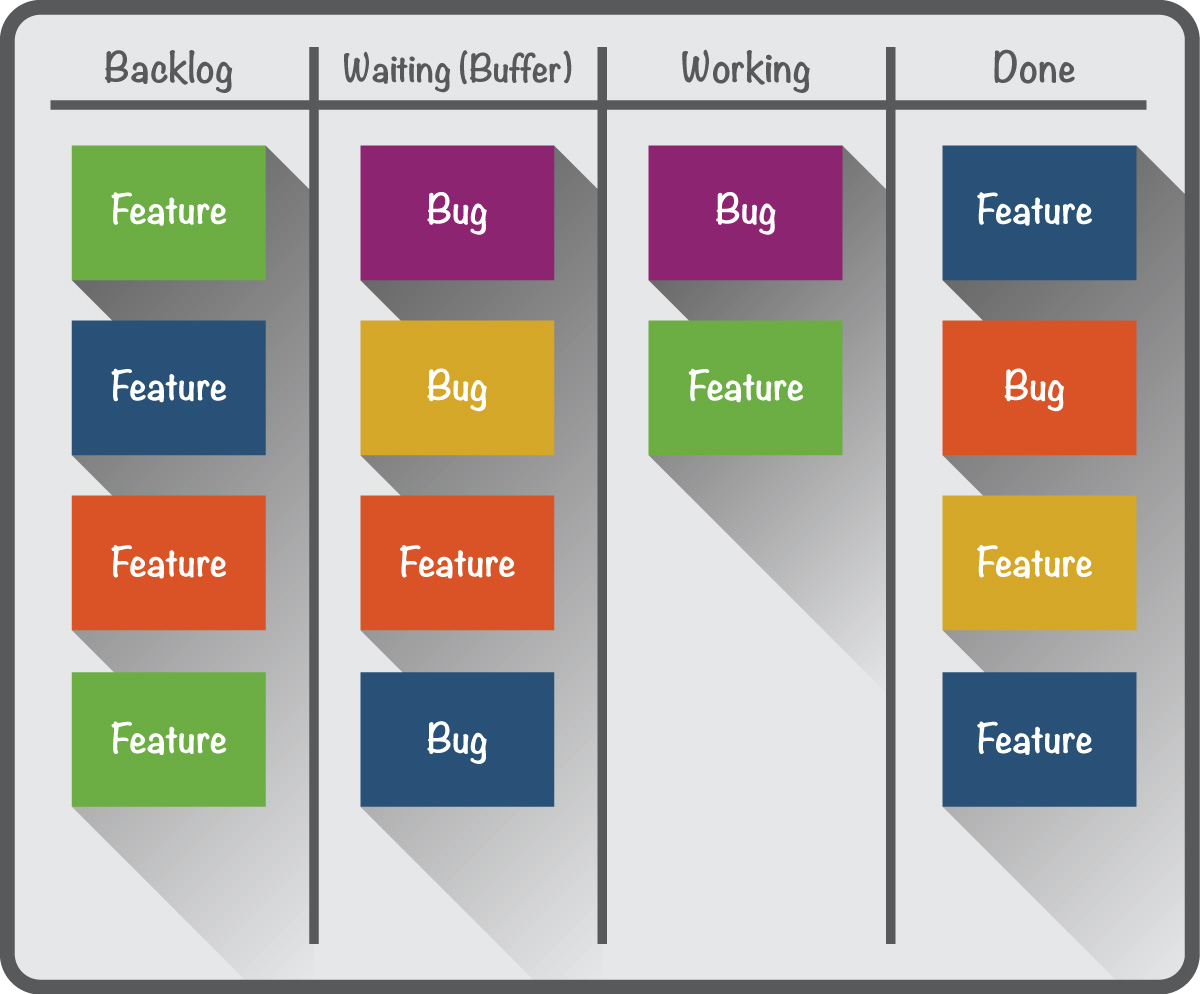
Continuous Improvement Is Intrinsic to Kanban Methodology
Kanban helps you get better and better at what you do by building continuous improvement into the model. You can track a few metrics to help understand your inefficiencies. Those most commonly followed by Kanban project managers include:
- Throughput - How many items can be completed in a specific timeframe.
- Due Date Performance - How many days an item is behind or ahead of scheduled completion.
- Blockages - How many logjams occur and how long they last.
- Quality - This can be represented by errors or defects in a time period.
For example, you might chart daily how many tasks are in each column of your chart or further downstream in your workflow. You can even classify how many are endangered, late, or critically delayed. Trends will soon emerge.
Advantages and Benefits of Kanban for Project Managers
Project management methods have proliferated – including PRINCE2 and Six Sigma – but more projects are failing, according to the Project Management Institute’s (PMI) 2016 “Pulse of the Profession.” This means companies are losing money on many major initiatives, and PMI found fewer than half of projects were being completed within budget and meeting their original objectives.
We’ll discuss shortly how Kanban compares to other project methodologies, but for now suffice to say that PMs are gravitating to Kanban because of its success in overcoming some shortcomings of other frameworks. These include difficulty scaling projects to enterprise level and coordinating multiple teams.
Kanban practitioners cite advantages including:
- Higher efficiency
- Reduced waste
- Better communication
- Faster problem solving
- Easy to implement
- Flexible
- Improved quality
Specifically, Kanban teams say the board makes it easier to figure out where their project stands, who is doing what, and what each member needs to be doing right now. WIP limits keep throughput high.
Jim Benson, Chief Executive of Consultants Modus Cooperandi, says by using visualization Kanban helps answer nine key questions including what is being built, what is stuck, who needs help, what has been finished and when results are expected.
Kanban vs Scrum: How Do They Compare?
Most practitioners consider Kanban to be one form of Agile, a philosophy of iterative product development that contrasts with traditional product development frameworks, such as Waterfall, which depend on sequential developments. A closely allied movement is Lean, which also grew from Toyota manufacturing practices and has among its core principles to: eliminate waste, amplify learning, decide as late as possible, deliver as fast as possible, and empower the team.
The most famous Agile technique is Scrum which is organized around a work sprint - a set period of time, usually two to four weeks – during which the work happens. It entails some rules, roles, and structure on how the team operates. There’s a strong emphasis on team self-organization. Kanban is less structured and more adaptable than Scrum and has fewer rules. You can apply Kanban principles to any process you have in place. Rather than being time boxed like Scrum, Kanban limits the amount of WIP to drive change.
Determining if Kanban is the Right Choice for You
The general wisdom for project managers looking at new methods is that if an organization needs a radical change, Scrum may be a better choice. If you have some processes that are working well, Kanban will enable you to improve over time without disruption of massive, sudden change.
Scrum, with its strict time limits, is seen as a more natural choice for teams who have critical timelines that must be met. Coach David Hawks of Agile Velocity recommends asking some key questions to determine if Kanban is right for you. He says Kanban is well suited to teams whose priorities change often, can break work down into small, similarly sized chunks, and have a strong culture of continuous improvement.
Opinions on this are divided, Anderson says that there is considerable evidence from published case studies that it is not necessary for work to be broken down into small, uniform units, and that in fact Kanban works well for work with a mixture of sizes, complexities, and urgency.
Hawks finds that Kanban is a good choice when the top priority is being responsive to customer needs because it has the flexibility to reduce batch size and cycle time. It is also well suited to organizations with a limited appetite for change and low need for ceremony.
“As for my personal wisdom, I like one saying: If you want to try Agile and can't figure out Scrum, try Kanban. It's a great stepping stone to build trust within an organization. It also sets the tone so that people can understand how a sprint cadence works in the world of Scrum,” said Brumbaugh of The Delivery Innovation Group.
“Kanban can be used in every vertical, but I have seen it work best in a product development environment. I would not use Kanban in a partnership or a place where stakeholders cannot agree to a … list of priorities,” Brumbaugh added.
Don’t Want to Choose Between Scrum and Kanban? Try Scrumban
As mentioned, Kanban is highly flexible and its principles can be applied to anything, even Scrum. As Kanban became more popular, Scrum teams interested in Lean and Kanban ideas began looking at how they could incorporate them, and hybrids were born, popularly called Scrumban.
Scrumban seeks to combine the best of both by adding WIP limits and visualization to Scrum. Scrum master Savita Pahuja recommends Scrumban for maintenance projects and event-driven work.
How to Implement Kanban
Does Kanban sound like something you want to try to implement in your organization? If you have decided to commit to Kanban, you need the following to get started:
- A board - physical or web-based
- Buy-in from senior leadership
- Training in Kanban techniques or a coach
- Commitment from project participants
Lawrence Roybal, Chief Executive of Oxford Solutions Group, who has coached healthcare companies on Kanban, recommends Kanban project teams of no more than nine people including any consultants. That keeps the group cohesive and the odd number of members aids decision-making. “It’s important that the group have the right make-up of participants including the end user and representatives from each part of the organization impacted,” he said.
“Before kicking off a project with Kanban, hold a planning meeting to determine if the project group has all the right participants to achieve success,” Roybal said. One of the most common mistakes is not getting early buy-in.
Prepare by Learning Kanban
If you run complex projects, using a coach, shadowing a team that is successfully using Kanban, and attending workshops and trainings will help you learn the ropes before trying to manage a project on your own.
“Training is a must and it should be experiential, meaning it should be more workshop and exercises, less slides and lecture,” said coach and trainer Michael Alexander of SolutionsIQ. “The aptitude and attitude determine the need for coaching. A team that is eager to learn and adopt new habits may not need a coach. A project manager that has a team that is averse to change will need a coach to help shape the Lean-Agile habits of the team.”
Common Pitfalls in Kanban Implementation
Moving to Kanban is not without pitfalls. A common mistake is trying to implement too much change at once, which flies in the face of Kaban’s evolutionary rather than revolutionary approach.
“Go slow; do a half mile not 10 miles in your first month,” Roybal said.
Other errors that Grumbaugh frequently sees are not having clear priorities and stalling work by moving it in and out of process. “In short, if you start the work, you should finish the work before moving on to the next priority,” he said.
In addition, newbies frequently get tripped up by not making it explicit what they are working on and what is not being worked on.
Preventing Kanban System Failures
Anderson of LeanKanban, one of Kanban’s leading authorities and creator of the Kanban Method used in project management, said that as Kanban has gone mainstream, new adopters tend to want tools and solutions to specific challenges, rather than wanting to join a movement as earlier adherents did.
He identifies two main reasons these project managers fail with Kanban.
- A knowledgeable project manager tries to introduce the framework to an organization that isn't ready for pull methods, and other important stakeholders aren't involved in the design. “Instead it is inflicted upon them and they aren't ready,” he said.
- Kanban is implemented initially, but fails to improve and take hold. This is generally due to a lack of Kanban knowledge and an initial focus “on low-value problems such as visualization and collaboration, but doesn't implement mechanism to create stress and motivation for further improvement,” Anderson said.
Anderson noted the first problem can originate with a coach who wants to demonstrate his or her own expertise and move more quickly than the organization is ready for. “The second problem is one of lack of knowledge and education on Kanban - a shallow understanding and a lack of training on the part of the change agent. In some ways, this can also be a result of arrogance, a belief that they already ‘know it all’ but in fact it isn’t nearly enough to insure a success and productive outcome,” Anderson said.
These articles were originally published by SmartSheet.com
Copyright 2018 © SmartSheet.com
10500 NE 8th St, Suite 1300, Bellevue, WA 98004-4357 USA